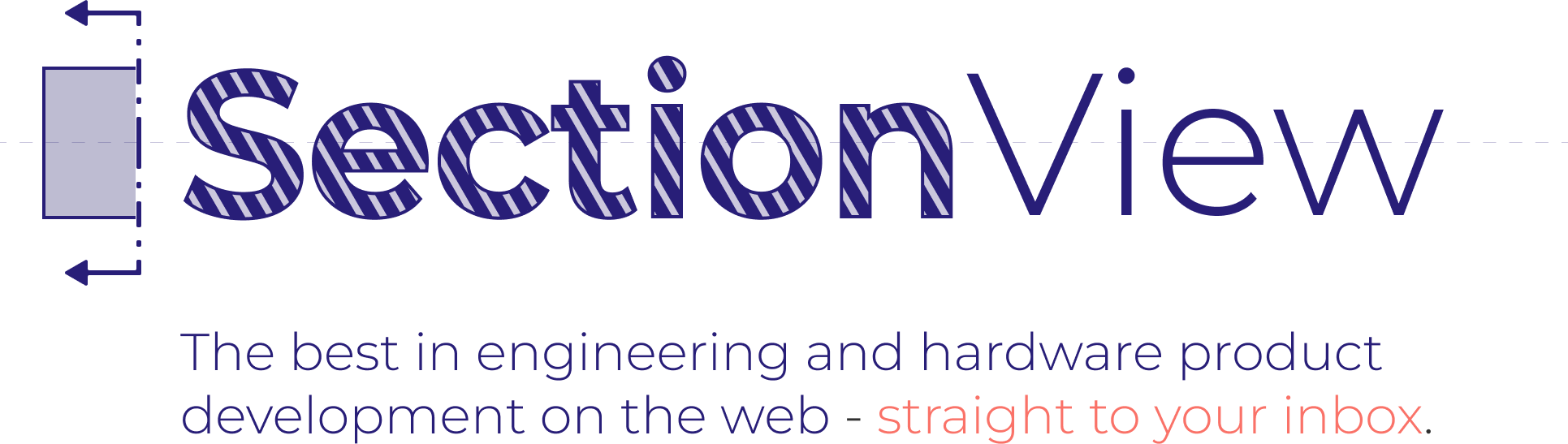
Section View: Issue #11
Welcome to Section View, a newsletter for curious engineers and hardware people. Brought to you with ❤️ by the Five Flute team.
The theme of this week’s newsletter is carbon fiber. As a design engineer, I was always intimidated by the prospect of designing composites. Anisotropic material behavior and huge amounts of variability in the manufacturing outcomes of composites structures have always scared the heck out of me. Over the years I’ve started putting more trust in composites as part of my design and manufacturing toolkit. Owning a full suspension carbon mountain bike helped me see how strong and flexible properly design composite structures can be, and how many applications are really suitable for composites. So in this issue of Section View, we’re going to take a deep dive into carbon fiber composites, …so grab your respirator and put on some nitrile gloves and follow me!
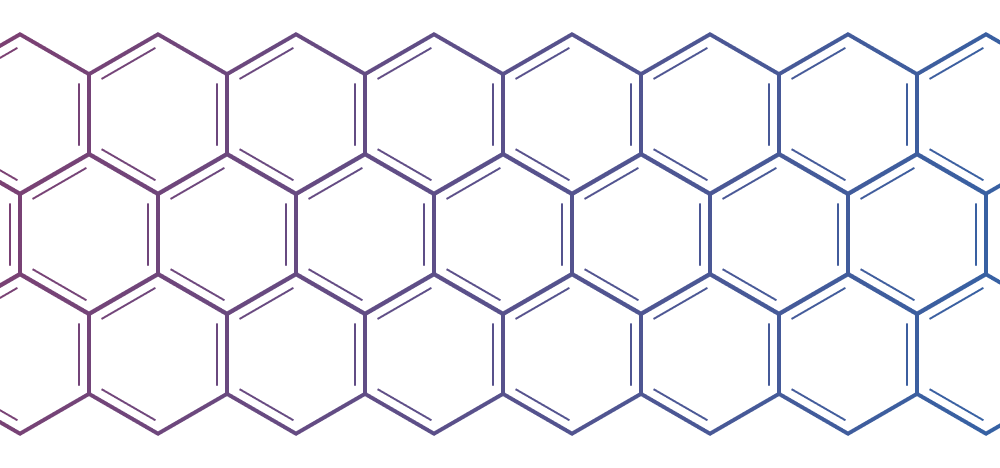
Manufacturing Spotlight
The amount of design best practices you can learn from watching a simple ‘How it’s Made’ style video is wild. The Five Flute team recently stumbled across this awesome Youtube video showing the manufacturing processes involved in constructing a fixed wing VTOL drone.
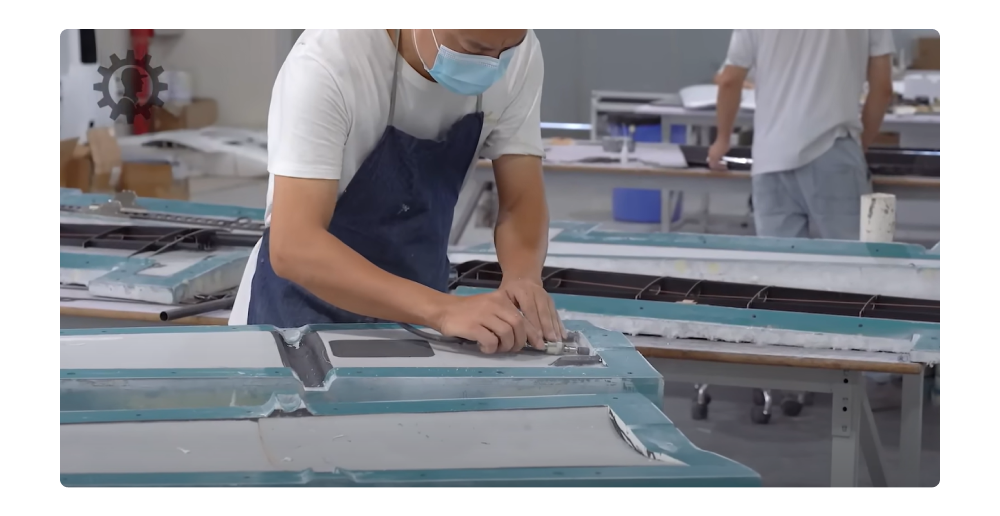
If you pay close attention you can learn quite a bit about proper mold design. My favorite part of this video is how the wing molds are used for both the wing skin layup as well as the skin-spar-skin sandwich assembly layup. There are lots of little mold design tricks that they use to index and locate internal spars and ribs.
Designer’s Corner
I gained a lot of confidence as a designer when I finally understood the ways in which multiple plies of carbon fiber can be integrated into a layup to achieve a desired stress response. But it took some time investment to learn! If the words balanced and symmetric layup don’t mean anything to you I recommend you pickup Design and Analysis of Composite Structures by Christos Kassapolglou. Chapter 3 is a particularly helpful and approachable overview of classical laminated plate theory, which should be reasonably well understood by any aspiring composites designer.
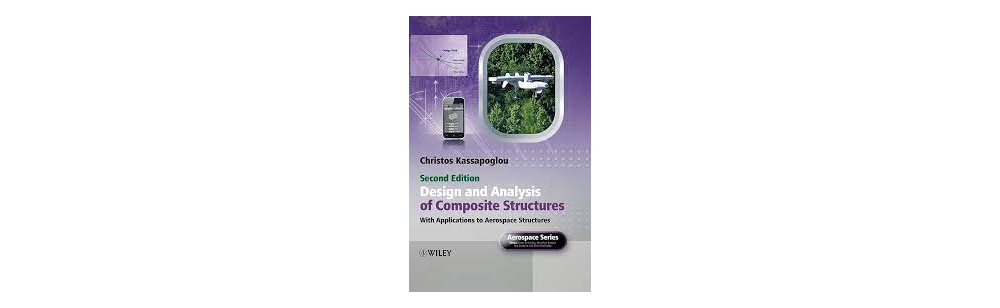
For a practical discussion of composites design, I really enjoyed this video on road bike frame design. Although I’m not sure I fully agree with the assertion that carbon and alloys shouldn’t be combined. Ever since I saw the carbon composite and titanium gearboxes that the Honda F1 team developed, I’ve had a soft spot for carbon monocoque layups with integrated aluminum and titanium components. I mean how cool does this look!
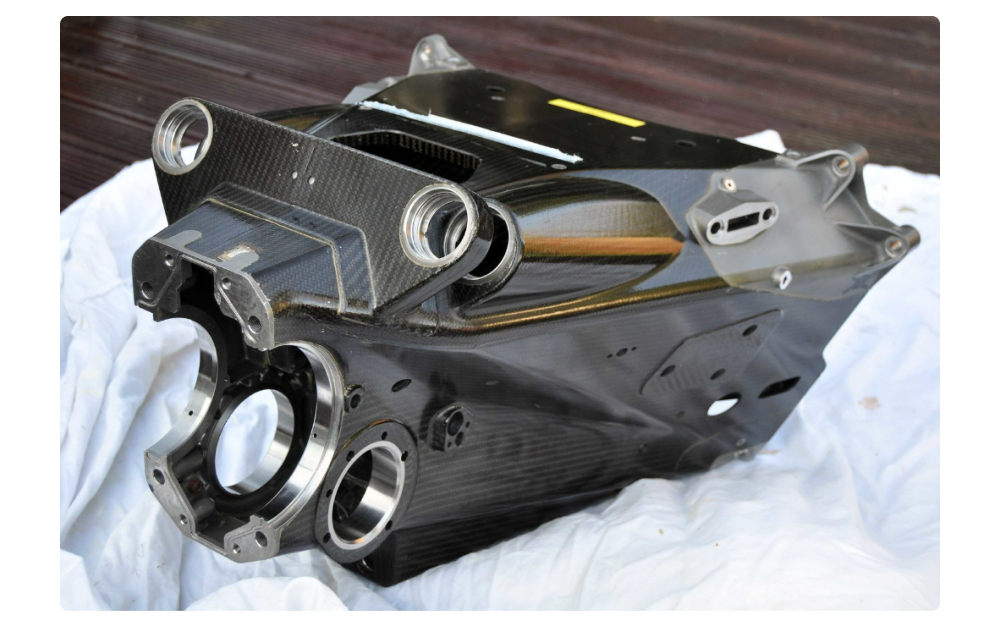
Failure Analysis
One particularly scary and intimidating aspect of carbon composites design is that failure modes are both harder to predict and more likely to be catastrophic. The ductility of metals offers advanced warning of complete failure in many machine designs, but the same luxury is not afforded to composites designers. When designers push the limits or don’t rigorously analyze and validate through physical testing, accidents can happen. As you are probably aware, the Ocean Gate Titan was a deep sea submersible with a pressure vessel constructed of a carbon fiber tube with titanium end caps. Unfortunately this submersible failed during a planned dive to the Titanic on June 18, 2023.
I’m highlighting this failure primarily to show the importance of physical testing and validation in any safety critical engineering situation. Failure modes are hard to predict and engineers will make mistakes during analysis.
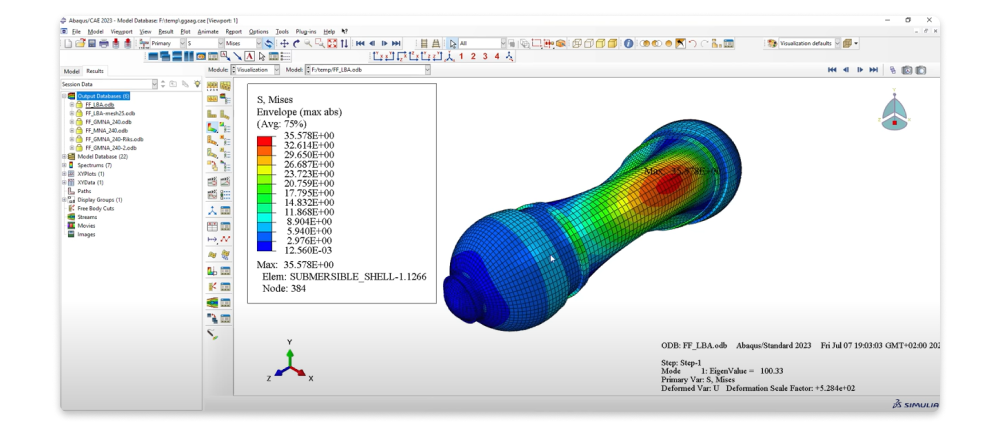
Physical testing is the only way to check engineering analysis and design assumptions in the real world.
If the Titan team had taken testing as seriously as the Look Bicycles team, perhaps this tragedy could have been avoided. Here’s a quick look at the HALT (highly accelerated life test) rigs that the Look engineers use to validate bike frame torsional stiffness and head tube deflection under load.
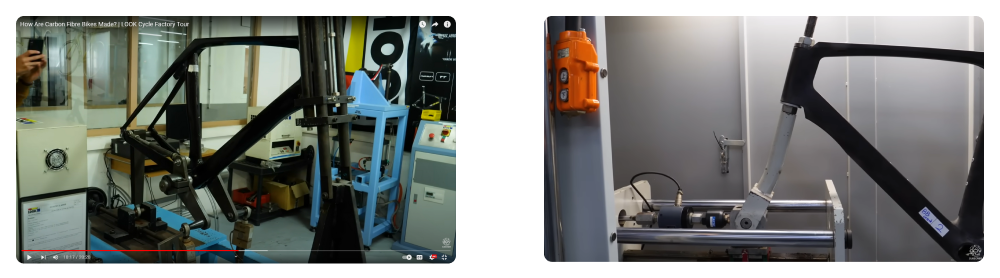
The bottom line is, if you want to be confident in real world performance of composite (and other hard to analyze) structures, you need to invest in testing.
Upcoming DFM Webinar Series
Given how much folks have been enjoying our DFM content on LinkedIn, we’ve been thinking about putting together a webinar (or two!) focused on process specific DFM guidelines for working design engineers like you. If you are interested in attending any of these webinars please let us know!