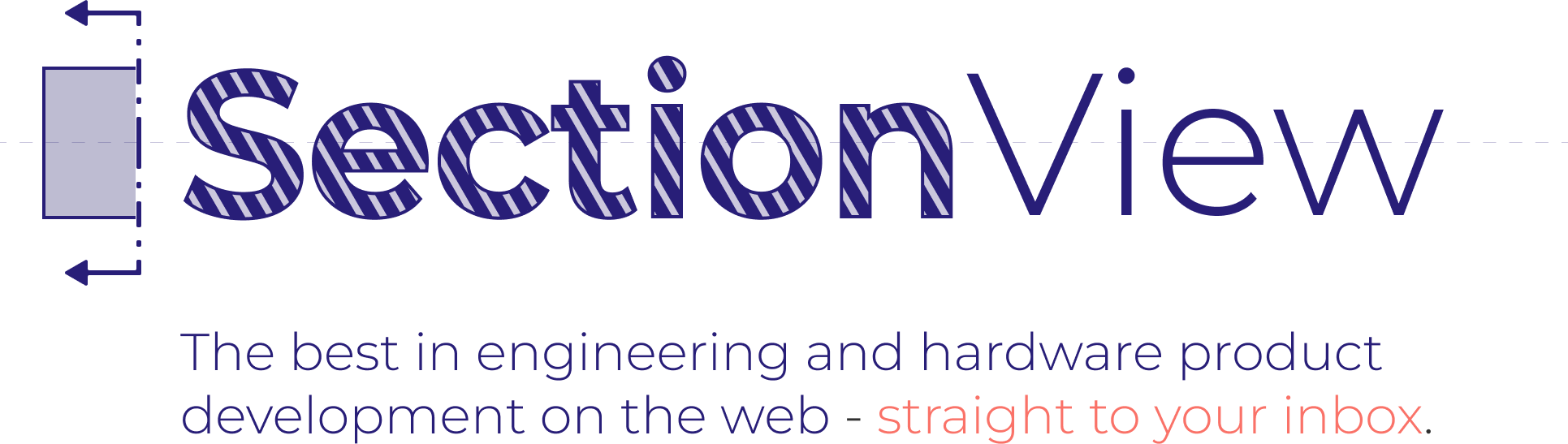
Section View: Issue #12
Welcome to Section View, a newsletter for curious engineers and hardware people. Brought to you with ❤️ by the Five Flute team.
In the past few months there’s been a lot of news related to the engineering of safety critical systems across the aerospace and automotive industries. In this issue of Section View I wanted to take a look at some of this recent news and see if we can learn anything about to help your daily engineering practice, regardless of what industry you work in.
Manufacturing Spotlight
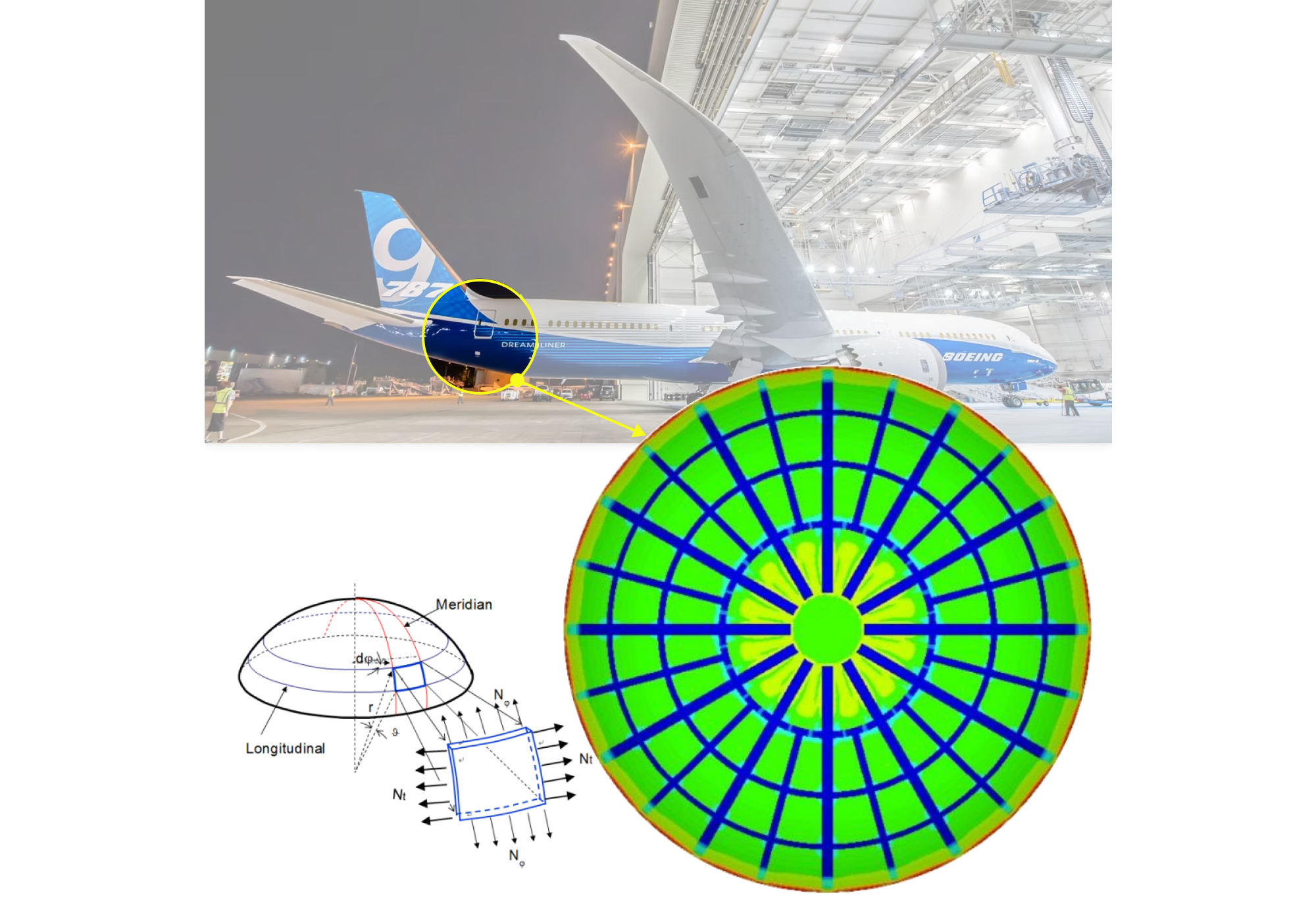
Spirit Aerosystems, a primary subcontractor of Boeing, recently discovered an issue with the aft pressure bulkhead on the 737 Max. Initial reports stated that pressure bulkheads had a bunch of extra holes drilled in them, but it seems now that the defect is related to hole elongation. What is hole elongation exactly?
An elongated hole basically has an oval or ellipsoid geometry. It can be caused by inconsistent alignment during drilling or by drill bits ‘walking’ during drilling.
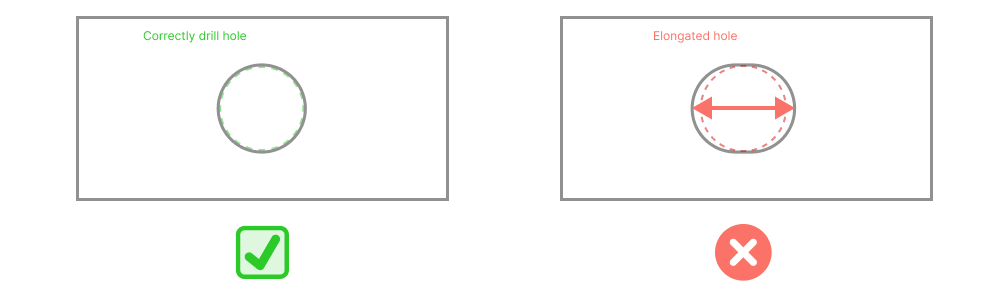
Having worked on boats and drilled thousands of rivet holes through my career I can tell you that it is very easy to accidentally elongate a hole when drilling thin sheet bodies. This kind of manufacturing defect can compromise strength and invalidate FEA because it changes the boundary conditions on rivets used to hold aircraft skins to stringers and other stiffening members.
The good news is that Boeing doesn’t believe that these defects put existing airframes at risk in the near term. This probably means that someone either used an appropriate safety factor in design, or they considered manufacturing defects probabilistically during design and analysis work. The lesson here is that despite how careful your quality control plan is, anticipating manufacturing defects can save you headaches later!
For more on rivets and rivet failure modes, check out our engineering guide on fasteners.
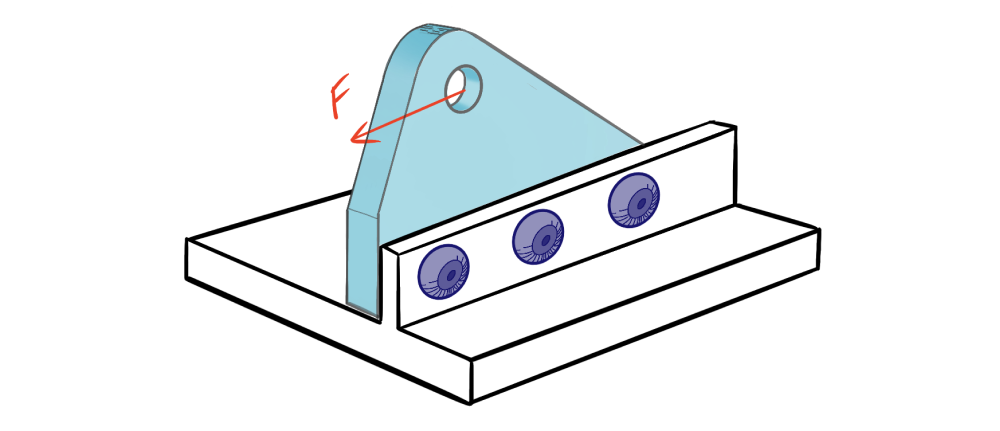
Failure Analysis

Recent accidents involving Cruise autonomous vehicles in San Francisco have led the California DMV to revoke Cruise’s operating permits in the state. I think this is worth highlighting because as engineers we care about failure modes. As the products and services we design become more complex and integrated across hardware, firmware, and software, the failure modes become more opaque and cross disciplinary. And this Cruise incident is a perfect example of how difficult automation actually is and how hard it is to develop test plans for validation. Despite driving 4 million miles previously with no accidents, the Cruise AV still managed to be involved in a crash and perform in a manner that is obviously wrong when compared with the behavior of any human driver.
Designer’s Corner
So what can we as designers do about predicting and preventing failure in complex products?
The good news is, the best methodologies for failure prevention have already been developed by the Aerospace industry over multiple decades of continuous improvement. I want to highlight three techniques that you can put in place on your projects today:
- Failure Mode Effects Analysis (FMEA). I like this video tutorial on FMEA from the CQE Academy youtube channel.
- Fault Tree Analysis
- Redundancy in safety critical applications. This video on the unintended acceleration failures of Toyota Prius and Camry models in the early 2000’s demonstrates how important it is to consider redundancy at every level. Long video but well worth it!
My favorite example of these techniques comes from aerospace. Airbus flight computers are quintuple redundant, meaning they have 5 duplicate flight control computers operating simultaneously and checking for agreement with each other. On top of that, these computers run two different versions of the control software programmed buy separate teams in two different programming languages, but all coded to the same spec. This kind of redundancy reflects a deep understanding of potential failure modes at all levels of the system, along with a healthy appreciation for the fault tree and fault overlap necessary to cause a serious incident. This is why aviation is so safe - the Autonomous Vehicle industry would do well to pay attention!
In Case you Missed It
We’ve added some awesome new content to our Engineering Resources page that you might find helpful.
-
Our Ultimate Guide to Sheet Metal Design pulls together every sheet metal article we’ve written into a comprehensive design guide available for download. Join the 305 other engineers that downloaded it in the last 2 weeks.
-
A lot of DFM guidance for CNC machining is cookie cutter and frankly not that helpful for experienced engineers. I think we’ve put out the most useful free content on CNC machining on the internet. Check it out yourself, I promise you’ll learn a thing or two even if you are super experienced!
That’s it for this issue, thanks for reading and good luck with your hardware projects!