Welcome to Section View, a newsletter for curious engineers and hardware people. Brought to you with ❤️ by the Five Flute team.
Happy New year from the Five Flute team! Thanks for being a Section View reader in 2023, we're kicking off '24 with a bang! In this edition we’re going to compare large scale and small scale manufacturing operations, dive into mechanism kinematics, and feature the most clicked links from 2023.
Manufacturing Spotlight
A Tale of Two Factories
In this week's manufacturing spotlight, I wanted to highlight the many shapes and sizes that manufacturing operations come in and how product quantity and scale drives everything. First, the Strange Parts YouTube channel has an excellent tour of the Carvera desktop CNC mill factory. A relatively humble operation cranking out small desktop gantry mills constructed from a variety of extruded and CNC machined components. The video features excellent coverage of bed of nails test fixtures, flex circuits, what a typical assembly line looks like, as well as giving you a great feel for the overall scale of the manufacturing operation.
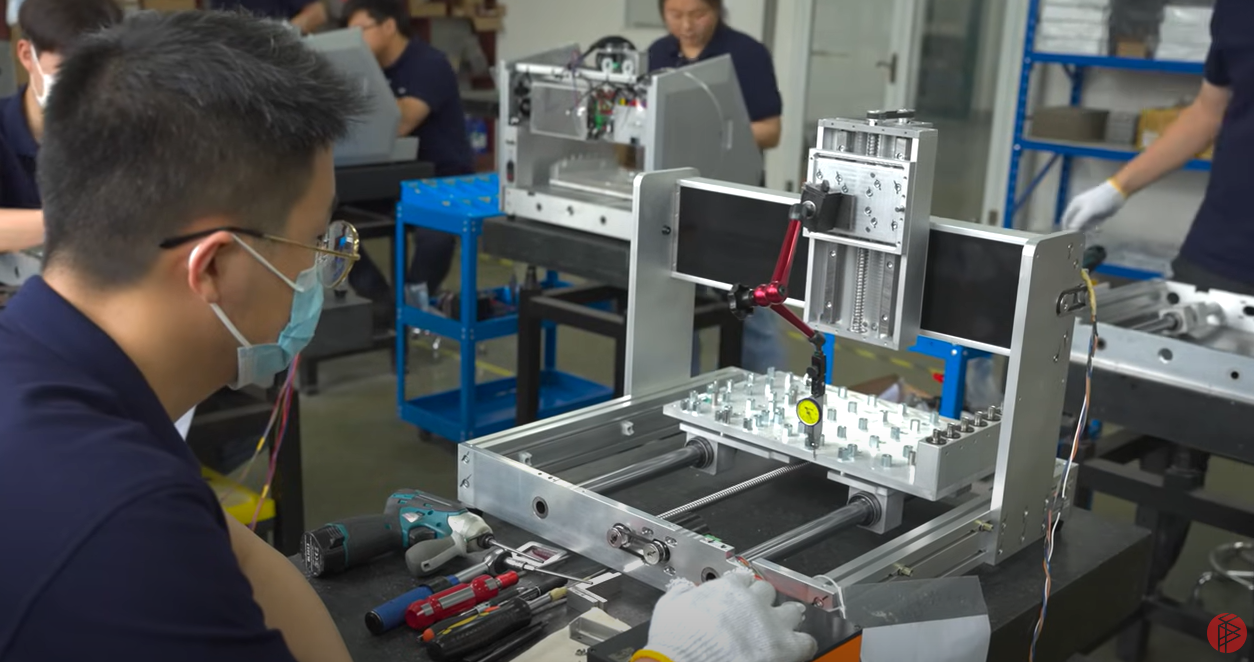
Contrasting this is Sandy Munro’s tour of the Tesla stamping line for the Cybertruck. It’s just completely ridiculous how much capital investment goes into just a handful of exterior parts for the vehicle. I loved this shot of the front door die used to form stainless sheet into an A class surface.
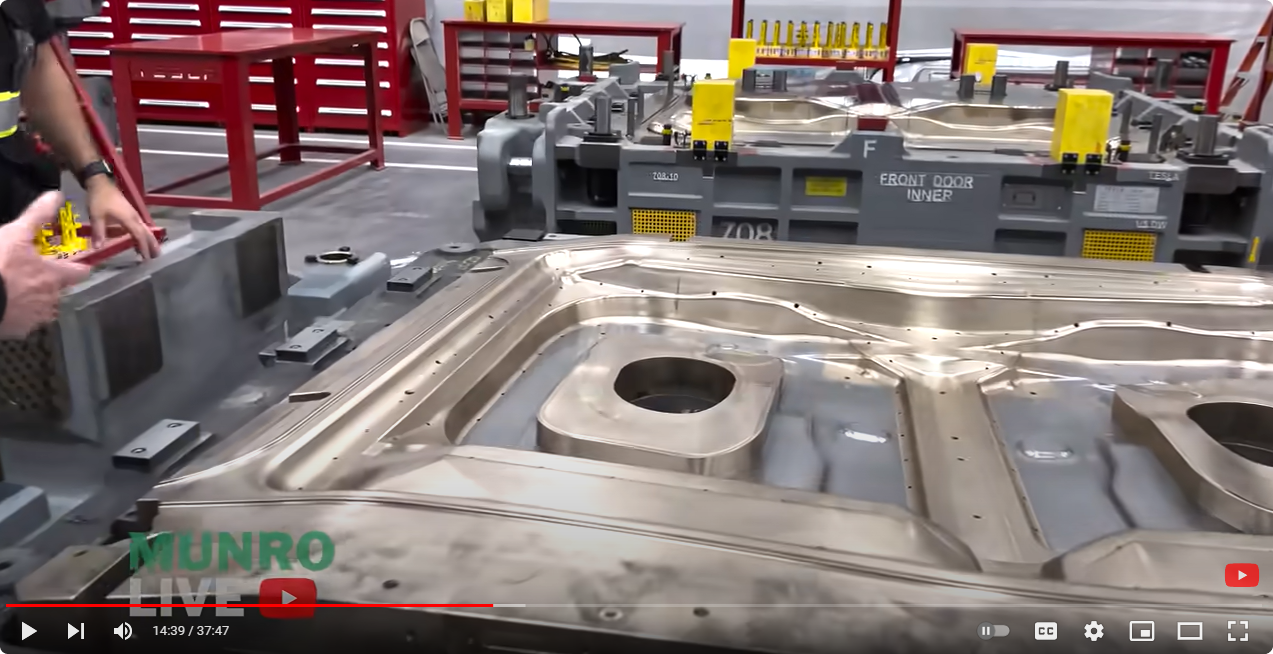
Surprisingly the entire die is made from aluminum bronze (not tool steel!) in order to prevent drag marks on the sheet surface. Aluminum bronze is actually used extensively in steel mills for its thermal, friction and wear resistant properties. I wonder how much the tool costs and how many parts it produces given the relative hardness of stainless steel.
Failure Analysis
Eight Bar Linkage Sensitivity
This week’s failure analysis looks at a worn out mechanism with interesting kinematics and design sensitivity. The front hood hinge on a Datsun 240 uses a very clever 8 bar linkage to allow for good hood clearance when open. Here’s a screenshot from the ***my mechanics insights*** restoration video (it’s basically ASMR for gearheads) that shows the mechanism in more detail. I’ve highlighted the linkages to help you guys visualize the motion profile. See if you can figure it out!
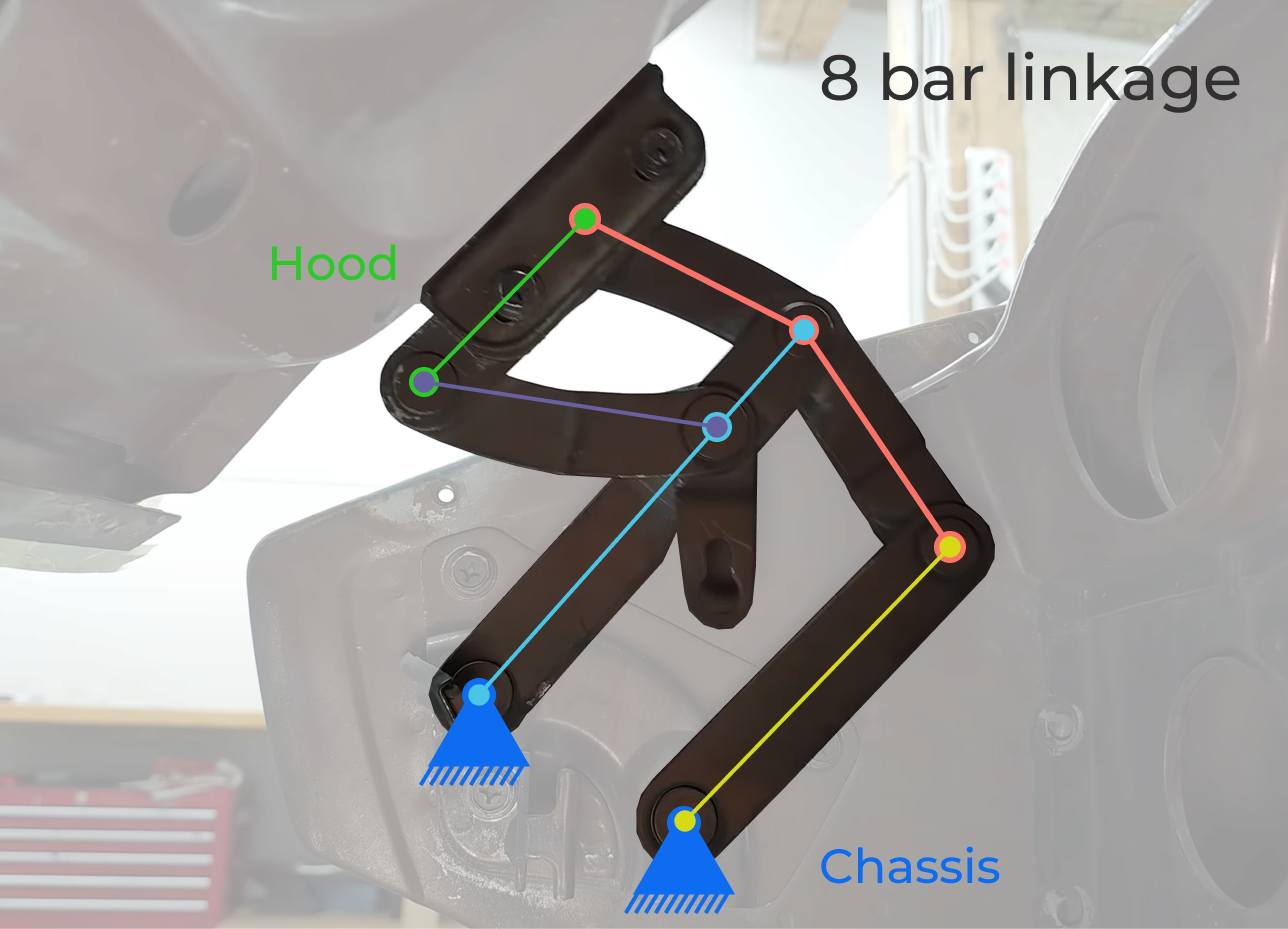
The reason why this is in Failure Analysis is the mechanism has wallowed out the rivet joints from continued usage, a somewhat expected failure for a 50 year old car. However, if you look closely this is a great example of design sensitivity that we can all learn from.
The amount of radial play at the worn out joints is relatively small, but the amount of overall deadband in the mechanism (free play in the position of the hood) is quite high. This means the mechanism is sensitive to small differences in position of the joints. This sensitivity is a key concept in kinematics that machine designers should work to understand both intuitively and mathematically. The same concept can be applied to manufacturing tolerances on critical kinematic systems, like a vehicle front suspension for example. For those of you looking to go a bit deeper on the subject, try deriving the position equations for each bar in the mechanism and represent it as a system of linear equations. You can solve this system using fSolve in MATLAB or Python. From there, try modifying the various points of the linkage to build your intuition around how the mechanism motion changes. That is the essence of sensitivity analysis. You want to understand how small changes in each individual system input will impact the overall output. For any multivariate system, the sensitivity can be analyzed by taking the partial derivative of the system with respect to each input.
Bonus points to this video for showing the zinc chromate conversion coating process, a great way to passivate steel parts and prep them for painting.
Designer’s Corner
While we’re on the subject of kinematics, we have a collection of awesome and very elegant kinematic systems used across robotics, medical automation, and the humble gas pump.
- LIMS2-AMBIDEX robotic elbow joint. An absolutely beautiful mechanical design with amazing machined components as well.
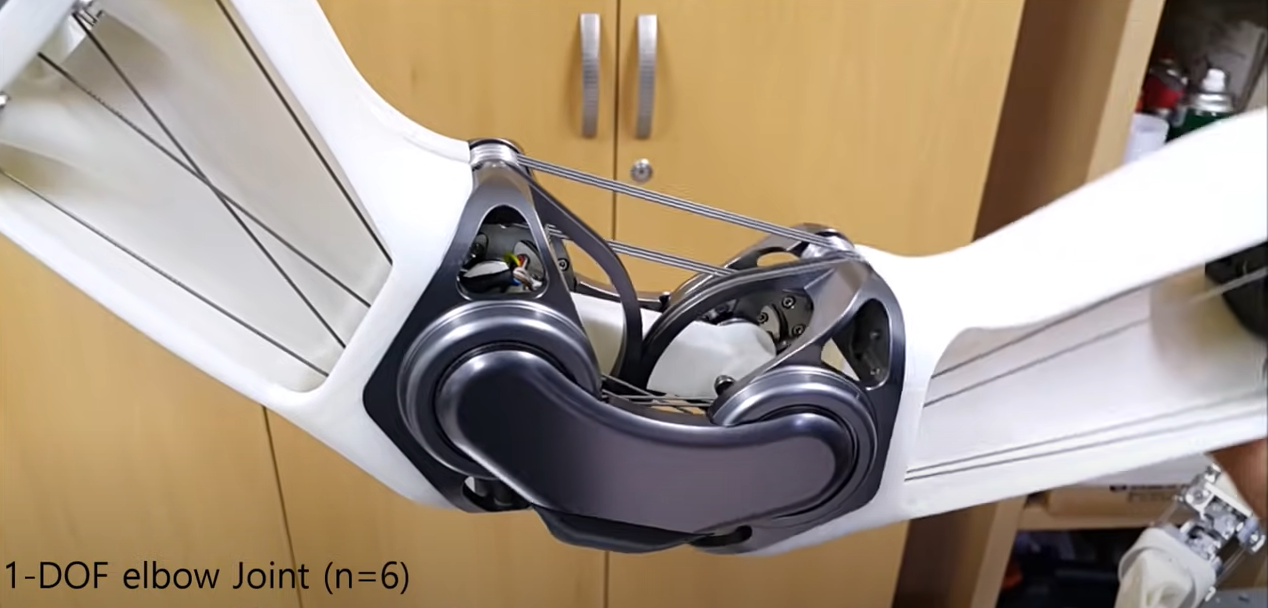
- Spherical parallel manipulation platform. A beautiful homebrew 3D printed version of an original design by the folks at NSK. Apparently this mechanism was originally developed to mimic the motion patterns of clinicians when performing cardiac ultrasound examinations.
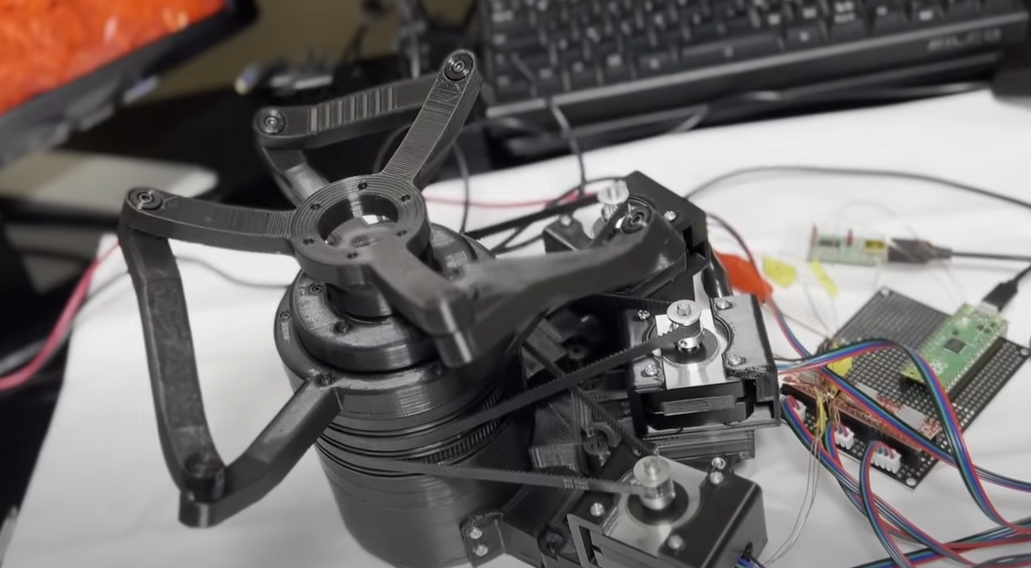
- Gas pumps. Steve Mould bought a gas pump with the goal of learning how they automatically turn themselves off when your tank is full. I just love the elegant simplicity of this mechanism and the breakdown of it’s functionality is very well done.
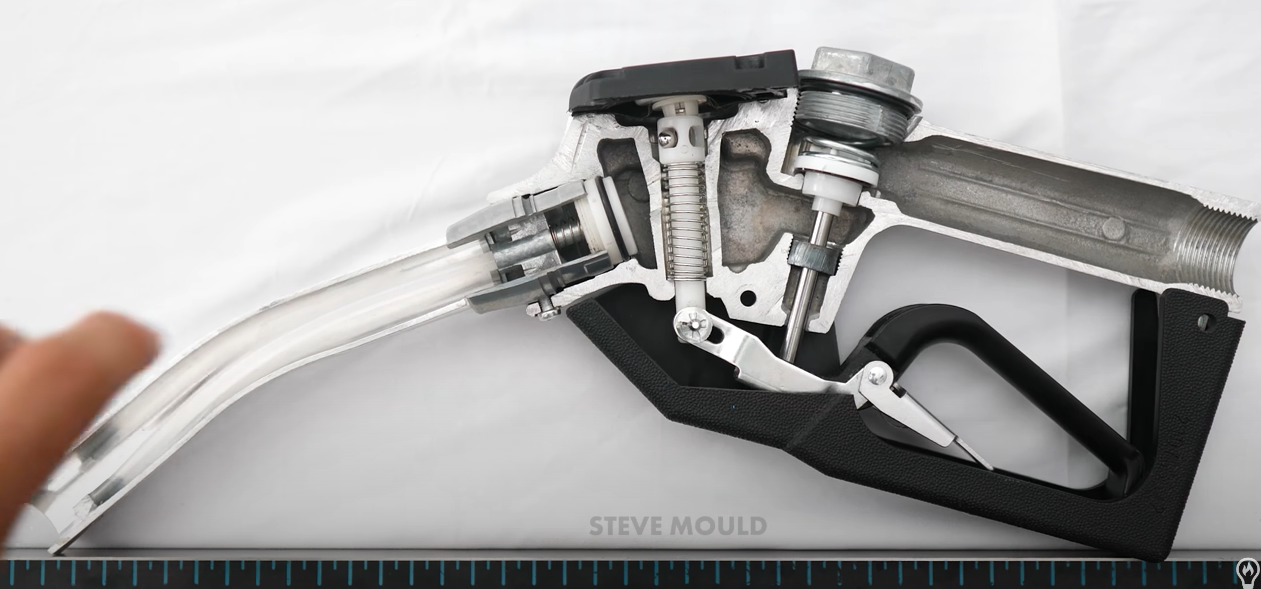
In Case you Missed It
Most Clicked Links from 2023
Here’s a quick look at some of the most clicked links from all issues of Section View in 2023.
Note: Five Flute works on mobile now! Apologies to anyone who previously tried to open a link to Five Flute drawings or models in our previous issues.
- Example drawing with top tips for DFM and drawing best practices.
- Our free FMEA template (Excel) along with this helpful how-to video on the FMEA process.
- Sheet metal DFM guide
- How to design great looking seven segment displays with the Bambu Labs 3D printer.
- How to build a carbon fiber plane
That’s it for this issue, thanks for reading and good luck with your hardware projects!