Welcome to Section View, a newsletter for curious engineers and hardware people. Brought to you with ❤️ by the Five Flute team.
Holy cow, February is almost over already and we haven’t put out a Section View in weeks. The good news is, we’ve been collecting some awesome links and writing a bunch of new helpful engineering content here at Five Flute. I’m stoked to dive in and share what our team is excited about and what we’ve learned from our engineering community this week.
Manufacturing Spotlight
Apparently the mysterious youtube algorithm can’t stop recommending videos on metal casting, despite the fact that I’ve searched for none of it (not that I’m complaining though). I’ve learned quite a lot in the past couple of weeks and I wanted to pass along some of the best videos I’ve seen.
Intro to sand casting
This intro video from the aptly named Casting the Future channel is a great primer on sand casting. It’s also a hilariously British intro to casting that describes the sand application as “just like making a rhubarb crumble topping.” This video features a nice overview of split patterns, mold cores, and basic mold preparation. I learned that the release agent or parting powder is just finely ground calcium carbonate (Ca Co3).
Andrew Martin has an amazing series of casting videos where one side of the mold is glass, allowing you to see the flow of molten metal through the mold.
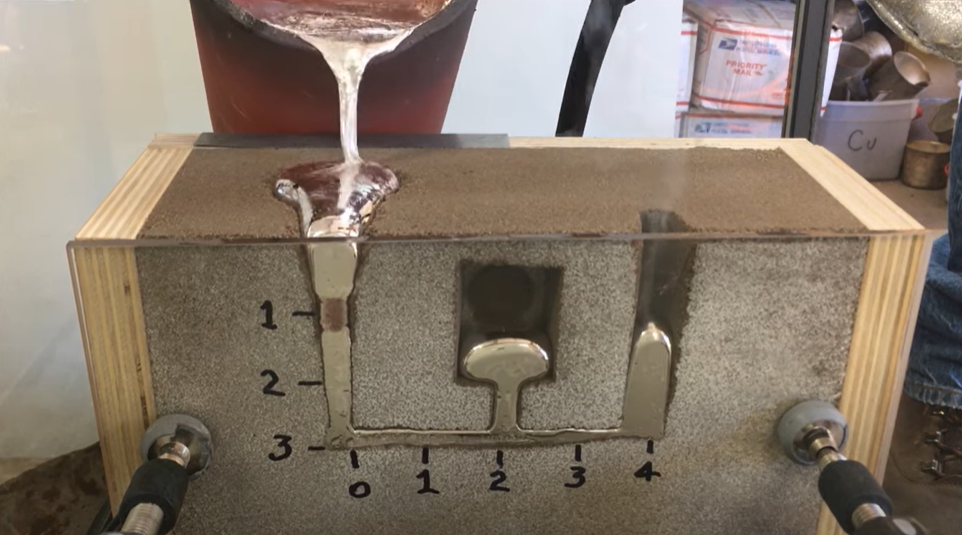
Lost Foam Sand Casting
I’m particularly intruiged by lost foam casting. Mainly because mold prep seems so fussy when you have split molds with sand cores, the prospect of just taking a foam positive, burying it in the sand, and pouring molten metal in to burn it away seems like such an easy way to make castings. This video from Wright Machining shows how easy it is to make a cast aluminum address sign (assuming you have a way to melt large amounts of scrap aluminum!).
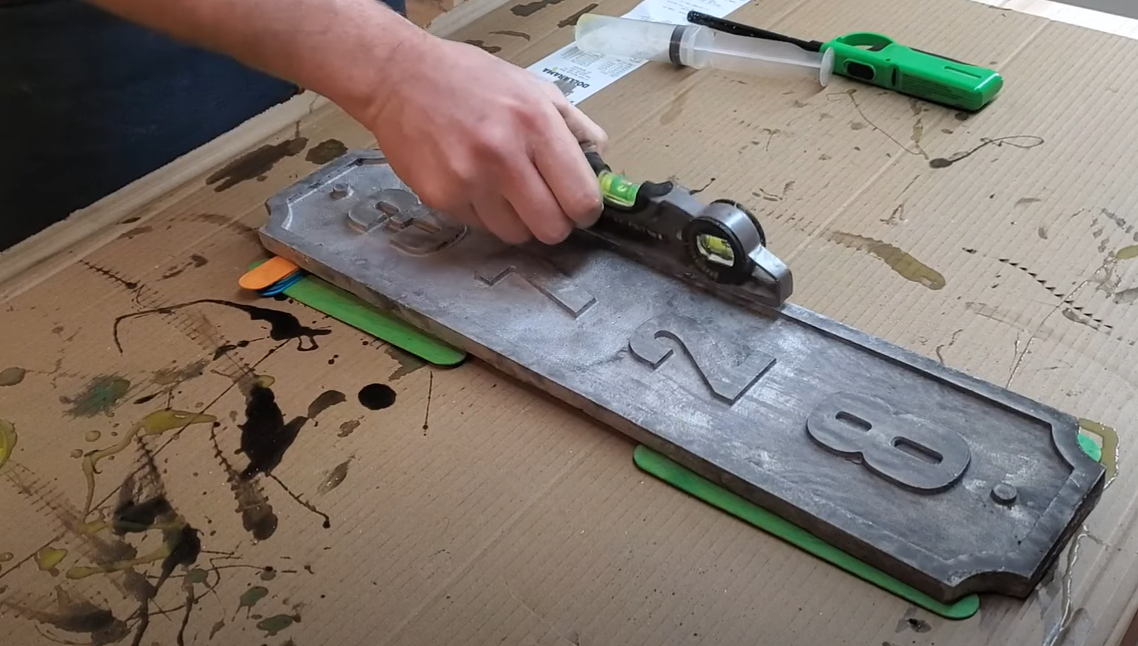
The Odds and Ends Machining channel has a great series on casting an engine at home. It’s particularly admirable as he does the post machining of the cast block components on a homemade CNC mill. I learned that the anticipated shrinkage when the casting cools is on the order of 1.3% by volume. Foundries have shrinkage rules associated with different types of materials, and (according to folks in the comments) you can use 5/16” linear shrinkage per foot for aluminum.
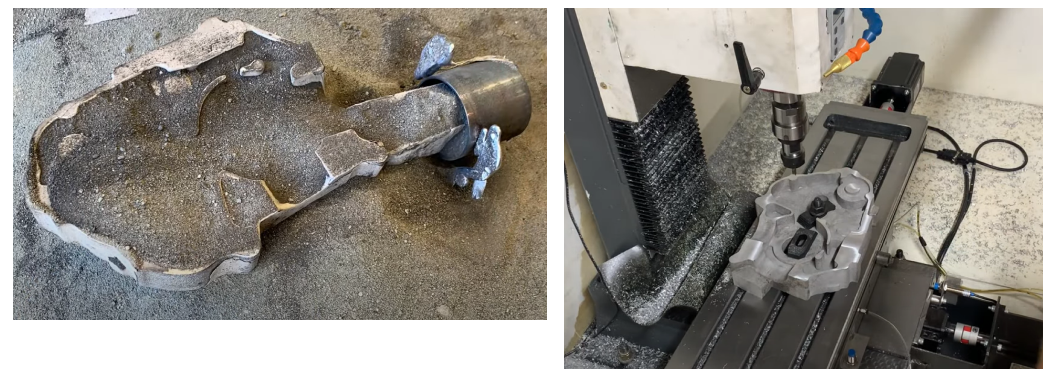
If you keep going down this rabbit hole, all roads lead to Kelly Coffield. This man is just insanely skilled at making high quality sand and lost foam castings at home. He also has quite the setup…
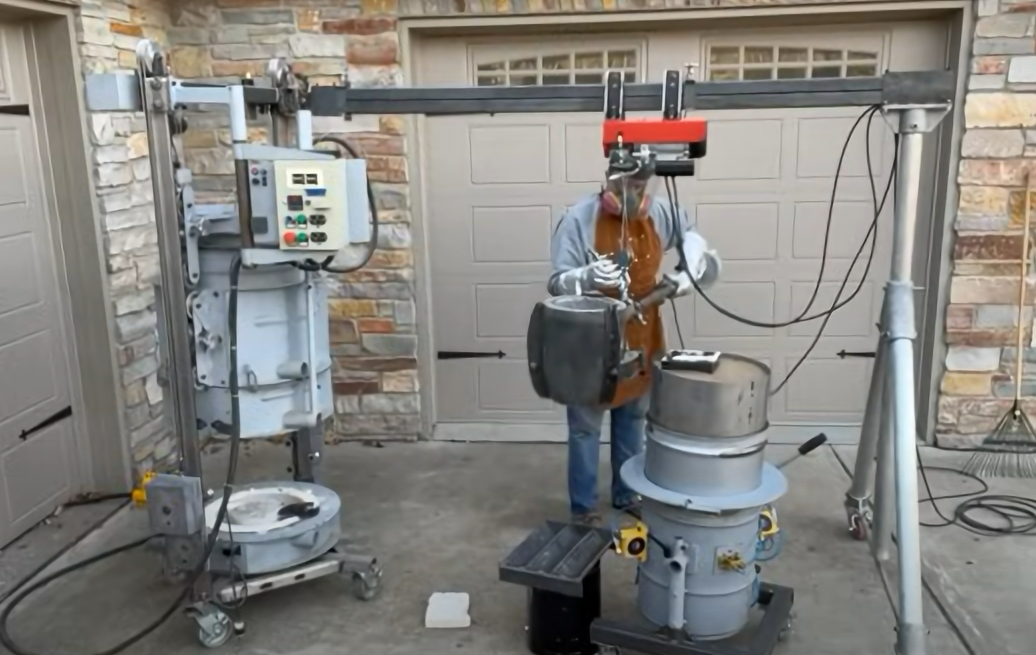
Yes thats a gantry crane attached to a 3 phase electric furnace. No you can’t do this at your apartment.
Kelly creates molds and cores of incredibly high quality and he gets amazing surface finish through the use of refractory coatings. Refractories are defined by ASTM C71 as "non-metallic materials having those chemical and physical properties that make them applicable for structures, or as components of systems, that are exposed to environments above 1,000 °F (811 K; 538 °C)". As far as I understand it (which admittedly is not very deeply, dear readers) the refractory coating on a lost foam mold maintains high strength when in contact with the molten metal, to the degree that (when supported by sand) it maintains a smooth surface finish despite the high temperature shearing action of the molten metal burning away the foam and flowing through the newly formed cavity.
Digital Foundries
Looking at how manual the home casting process is and how much work goes into mold preparation, I began to wonder how prototyping and low volume production is economically feasible. This led me to discovering the sand binder jet 3D printing process for molds and cores. This video from ExOne gives a nice overview along with a tour of a modern “digital foundry.”
Failure Analysis
If you do end up doing some home casting, make sure you don’t have any moisture trapped in the metal you add to your furnace.
On a more practical note, if you are designing, building, or testing cast parts you should be aware of the kinds of defects that can occur during the casting process. This fantastic video from the folks at Star Rapid goes deep on pressure die casting defects and how to prevent them.
Designer’s Corner
Two wheeled innovations
I feel like bikes are the gateway drug to engineering for a lot of mech E’s. The basic design is so elegant that its hard to believe it can be improved upon in any meaningful way. When I stumbled upon this string bike drivetrain design I wanted to hate it but its actually quite elegant in a lot of ways. The StringRide system uses Dyneema chord, combined with a clever arrangement of windlasses and cam actuated rockers to provide motive power to the back wheel.
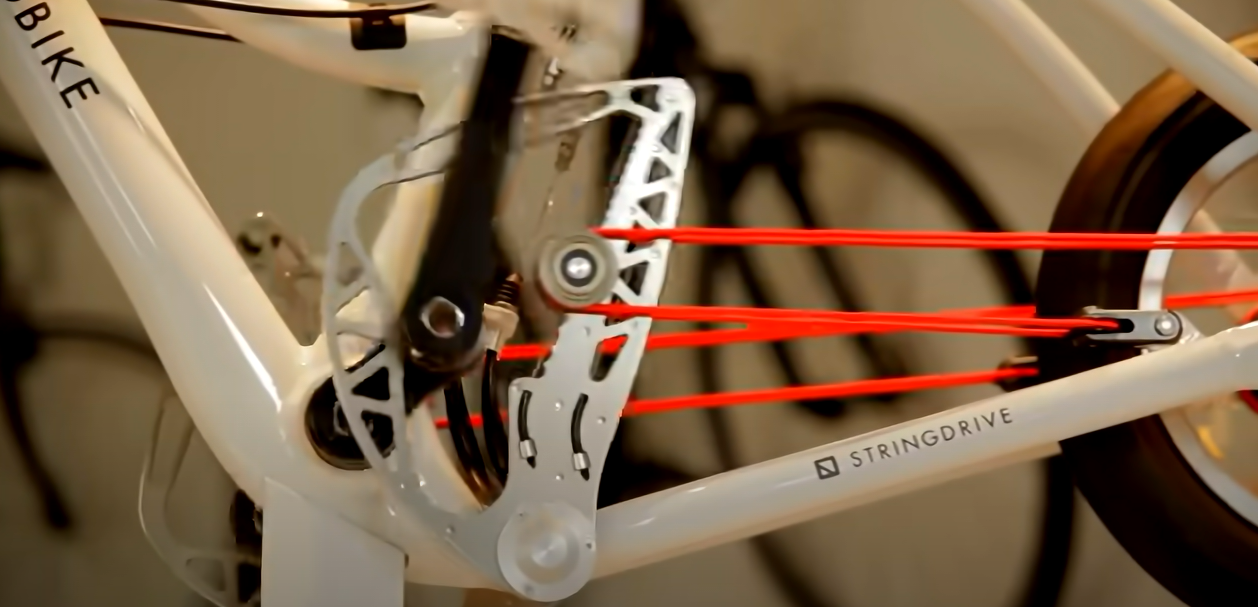
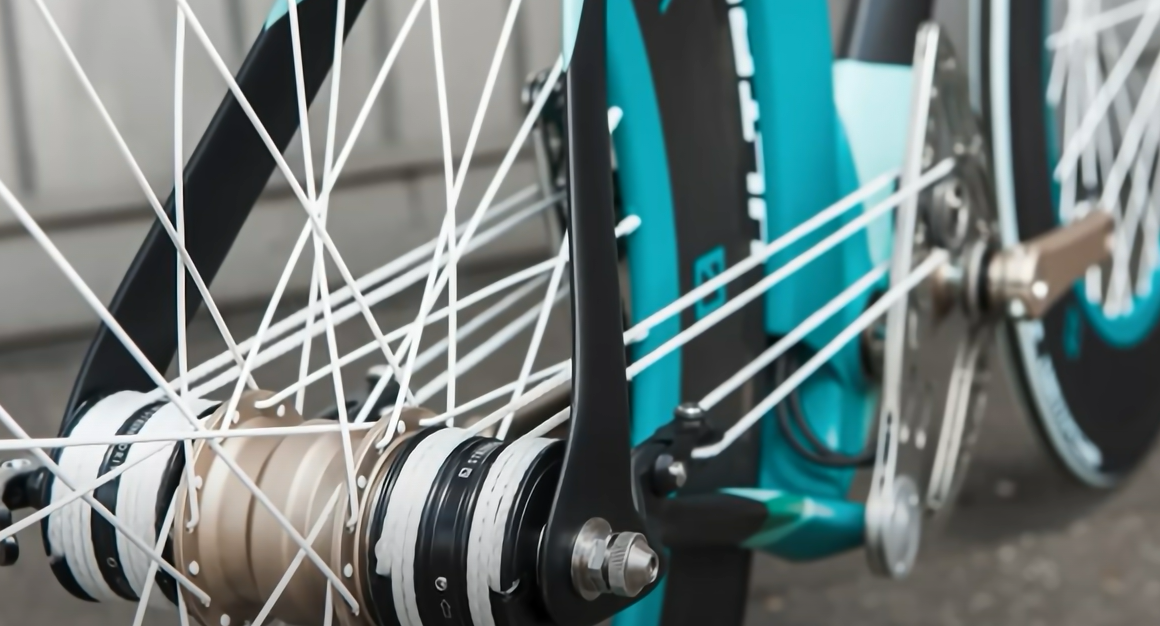
Side note: Dyneema is an amazing ultra-high molecular weight polyethylene (UHMWPE) that is used in climbing and rope access gear, safety equipment, marine applications and more.
Take a look at the kinematics of the CAM follower design. I particularly like how the cam profile enables a more efficient transfer of torque throughout the pedal stroke when compared to a traditional crank drivetrain.
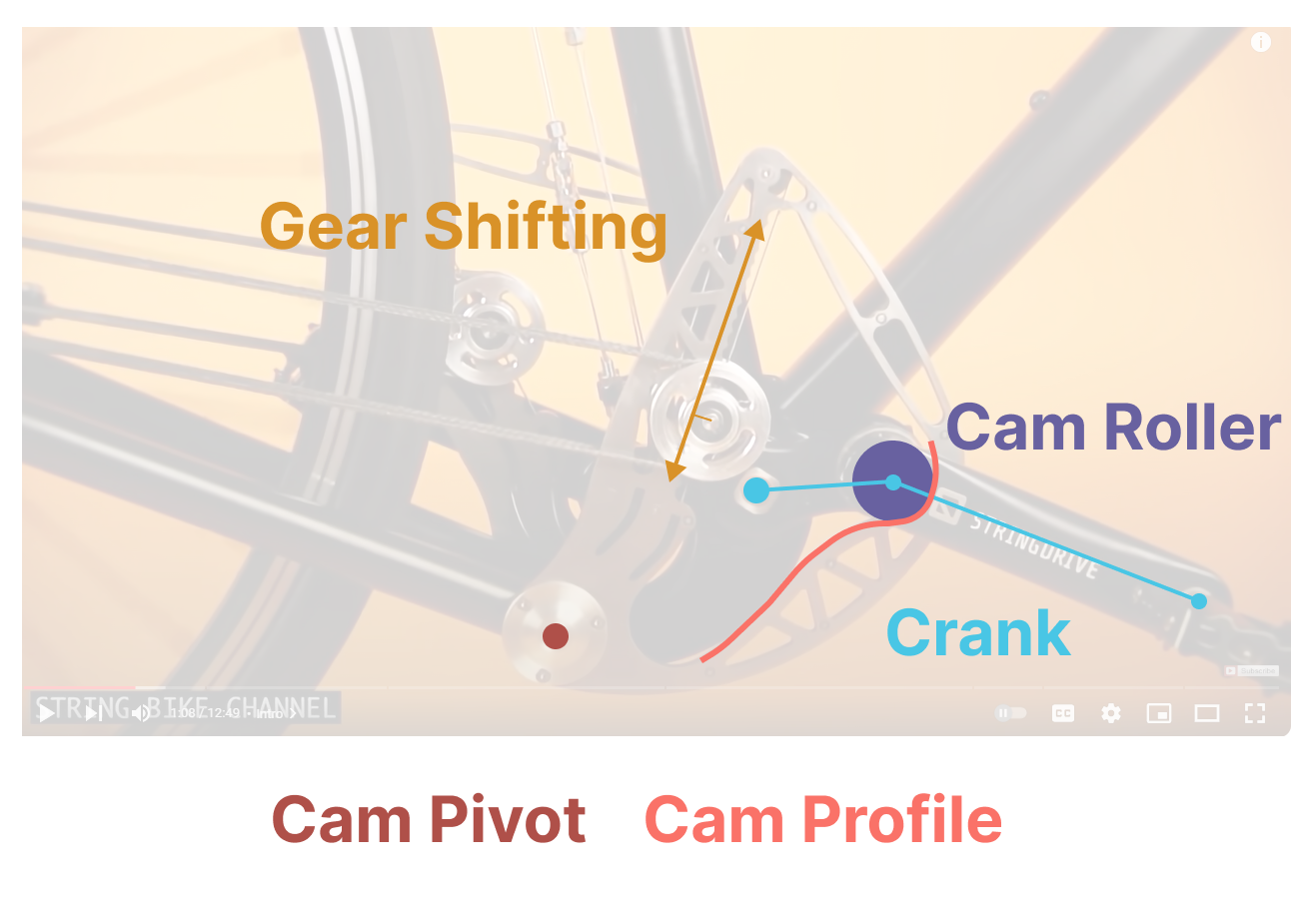
Back when Boeing was good at design
The recent issues with Boeing have been both scary and upsetting. I love seeing companies with strong engineering and design cultures succeed in the marketplace. The opposite is also true, and Boeing seems to be a stark reminder that culture eats strategy for breakfast. I hope that Boeing can find it’s way back to having a strong and deeply rooted engineering and safety culture, because America’s avaition industry needs Boeing to succeed. To that end, I’d like to celebrate the work that Boeing’s engineers did on the 727. It is just packed full of industry firsts and innovations. Here’s a short list, but the full video is worth a watch even for the non-aviation enthusiast.
- First tri-jet airliner
- First aircraft with triple slotted flaps (structurally very tricky to do!)
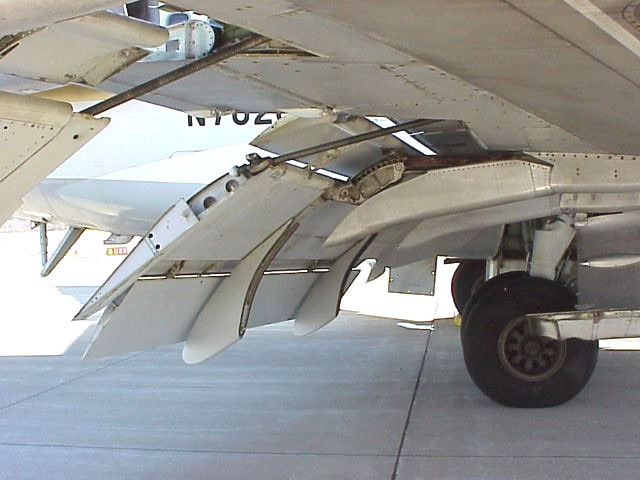
- The only large airliner with a nosegear brake
- First engine nacelles with perforated inlet liners for noise reduction
In Case you Missed It
Waterproof product design and battery enclosure knowledge from the community
Last week I dropped a new article on how to design waterproof products in our engineering guide. I ended up getting a bunch of positive feedback on Linkedin from the community, and even learned a thing or two about battery enclosure design. This knowledge comes straight from reader Nick Milanovic, a battery design leader at Accelera (Cummins).
“Battery enclosure seal design for automotive often needs to seal in conditions beyond - or in conjunction of - a static IP rating such as;
- Thermal runaway. Sealed joints must function under thermal runaway conditions where interaction effects of high temperatures, pressure spikes and volatile compounds expelled from the cell during the event must be managed to ensure you contain the gases and pressure to allow venting from the battery pack from a defined location. This is often the primary load case considered to size your seal geometry, material choice and overall strategy.
- Grounding. Sealed joints often need to be designed with electrically continuity in mind for grounding. It’s not recommended to rely on a threaded bolt to do this and you can use an internal strap if you want to decouple the function, but often you can integrate this in the seal via conductive gaskets or ensuring metallic contact surface on the joint.
- Seal displacement under mechanical loading. Depending on the structural requirement of the battery, mounting condition of the pack in the vehicle and seal compliance, you need to ensure IP rating in worst case displacement conditions (I.e - chassis/pack torsion or bending). Adhesive joining technology can be used to increase both pack stiffness and sealability in this case but can contradict with the next consideration - serviceability.
- Serviceability. This translates to service process time and number of times you can re-use/reapply the seal. Fundamentally batteries are much less service intensive than traditional combustion technologies but at Accelera we consider this to still be a crucial attribute for some commercial vehicle applications to ensure low TCO. The desire for a “sealed for life” pack is possible and can be achieved with consequence, but depending on the use case of the customer, their need for minimising downtime and the environmental benefit of maximizing battery pack life instead of replacing at a pack level and scrapping it for recycle when a component fails, if you can design to make the pack serviceable at the same cost, why not!?”
Five Flute customers in the news
Five Flute customer Harbor recently launched their new baby monitor system, led by the extremely talented engineer (VP of Hardware) Sean McBeath. I also gave a shoutout to the engineering team at Freight Farms with our latest customer story. Since adopting Five Flute for drawing reviews, they’ve found and corrected over 4000 issues with their assembly and part drawings. We’re super honored to have helped make the leading AgTech product that much better.
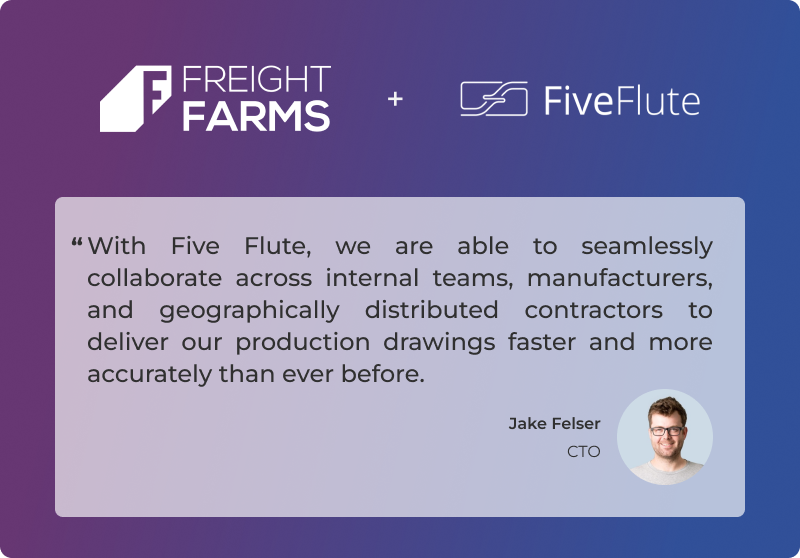
If you want to learn how Five Flute can help supercharge your design and drawing review process, sign up for a demo with me . :)
That’s it for this issue, thanks for reading and good luck with your hardware projects!