Welcome to Section View, a newsletter for curious engineers and hardware people. Brought to you with ❤️ by the Five Flute team.
Manufacturing Spotlight
Improve your drill press
This week we’ve got a cool improvement for all of your home shops out there. The humble drill press is one of the first tools in any woodworking or metalworking shop. It’s also one of the sketchiest tools in terms of work holding. Drill bits have a tendency to grab soft materials (and the vise) and fling the workpiece across the room at high speed. If you’ve ever seen this happen in a college machine shop you know how terrifying it can be.
To solve this problem, you can use a float lock vise. This float lock vise adapter design from the Pask Makes YouTube channel is just brilliant. It is so elegant and simple to use!
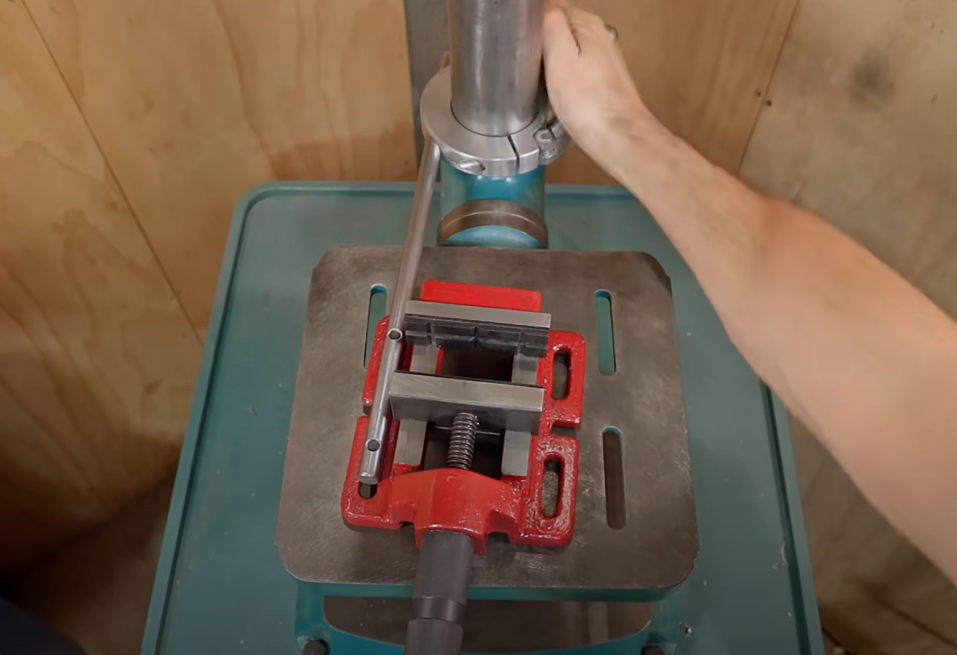
I like it so much I went ahead and designed my own. This is very much a work in progress, but if you’d like to take a look at it you can check out this Five Flute 3D model review. I’d love your feedback on it!
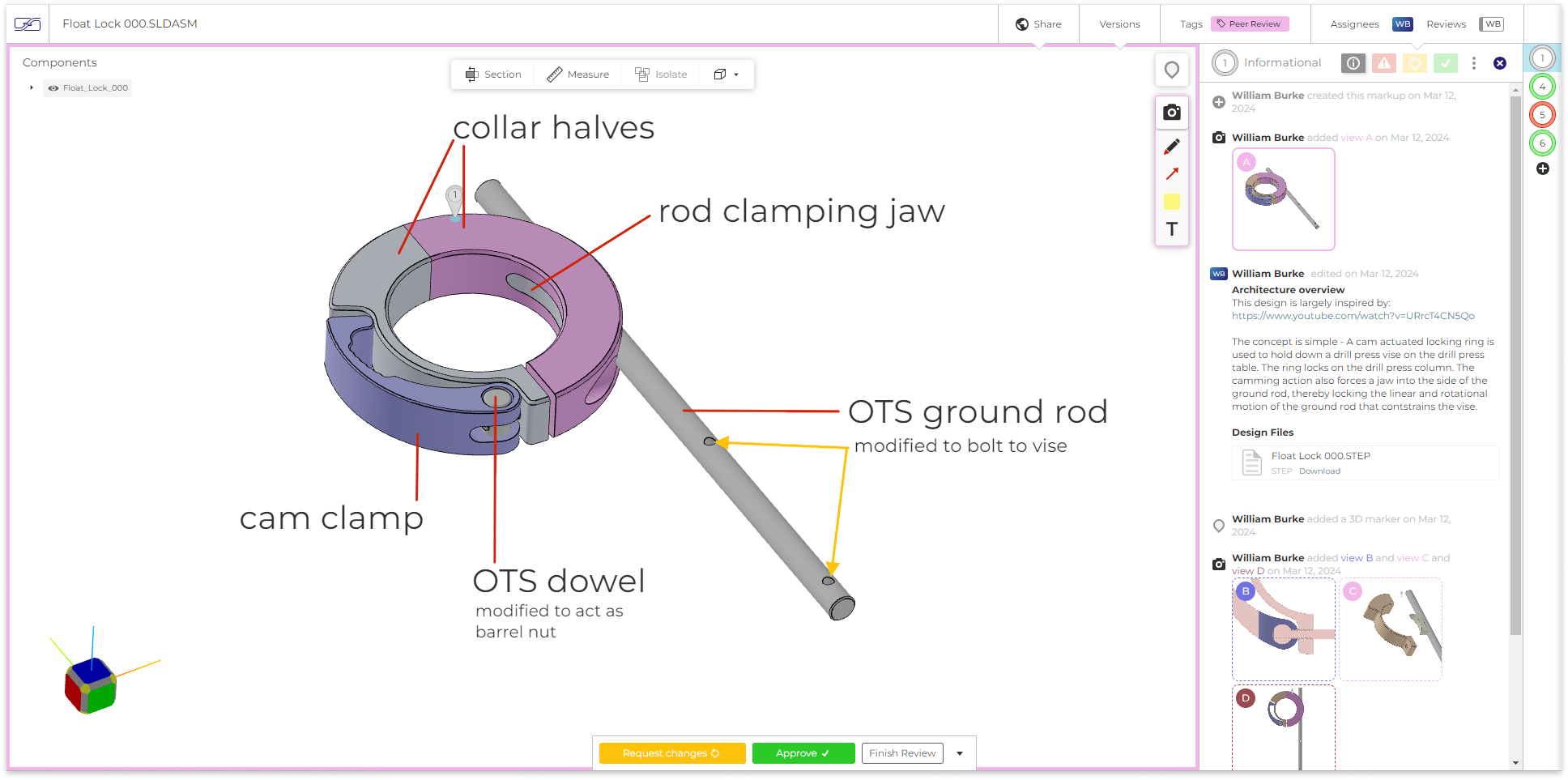
Anodizing at home!
The Iron Forest Knives channel has a great feature video on how they achieve fantastic anodizing results with a relatively humble “home gamer” anodizing setup.
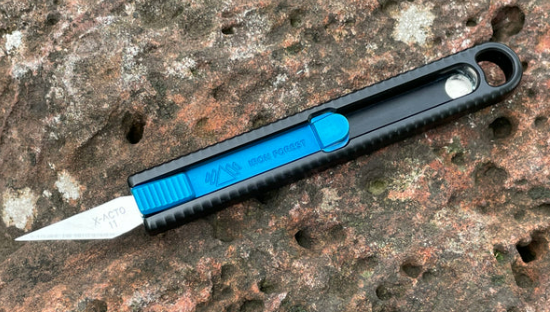
I like this video because it’s effectively a miniature industrial workflow that is a great primer on process parameters and how to ensure high quality coating formation.
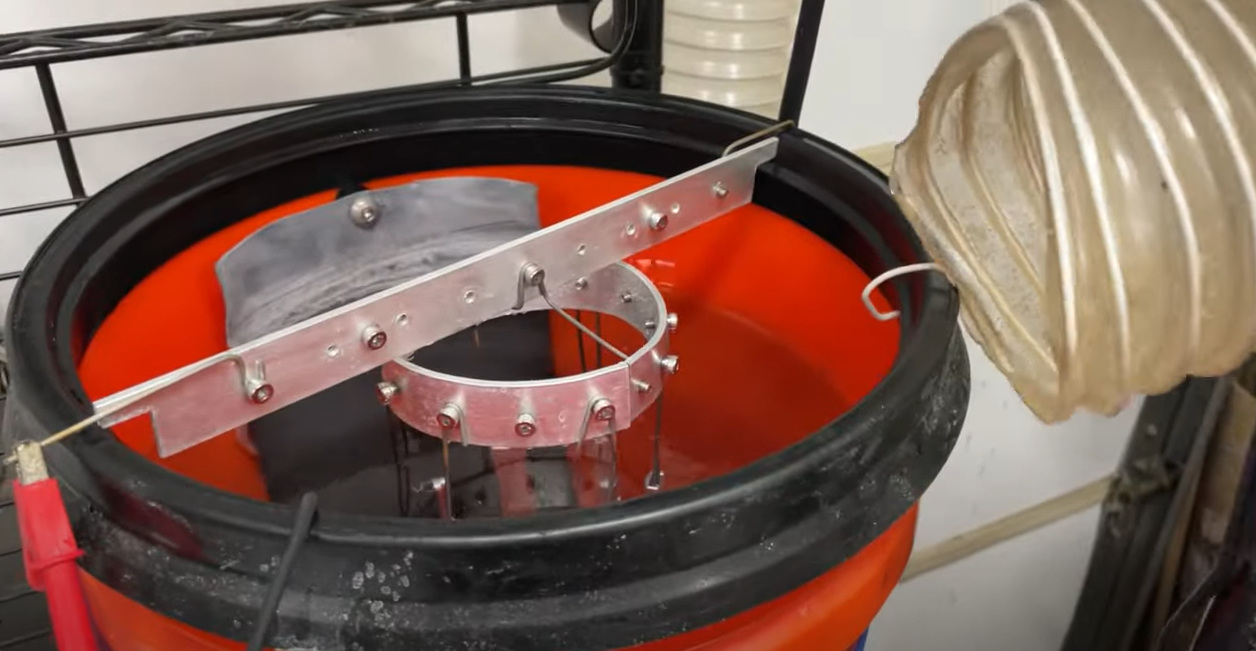
They also link to a Google sheets calculator for computing current density during anodizing! Nerdy goodness. If any of you dear readers do some anodizing at home I’d love to learn about it and feature you in this newsletter!
Failure Analysis
3D printed handlebar failure
At the 2020 Japan Olympics, a custom 3D printed handlebar on the bike of Australian athlete Alex Porter broke during the team pursuit race. Naturally he crashed and it wasn’t pretty.
The folks over at DFAM have a great feature article on this in their Bits to Atoms newsletter.
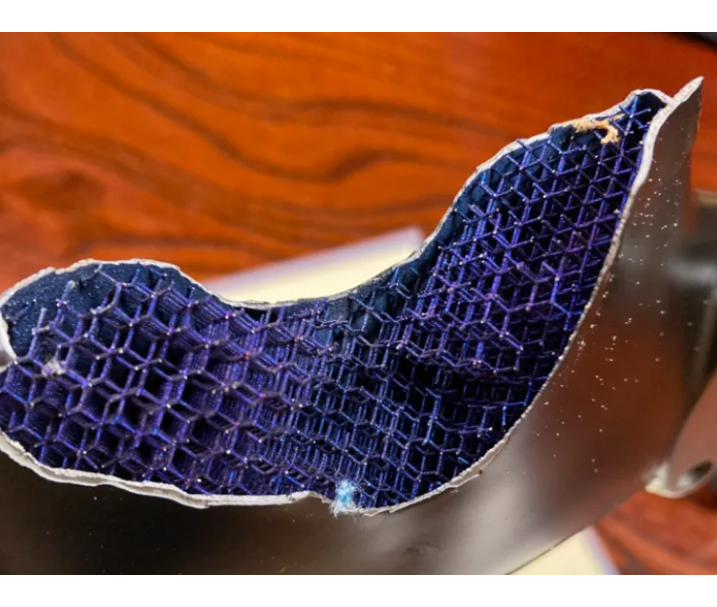
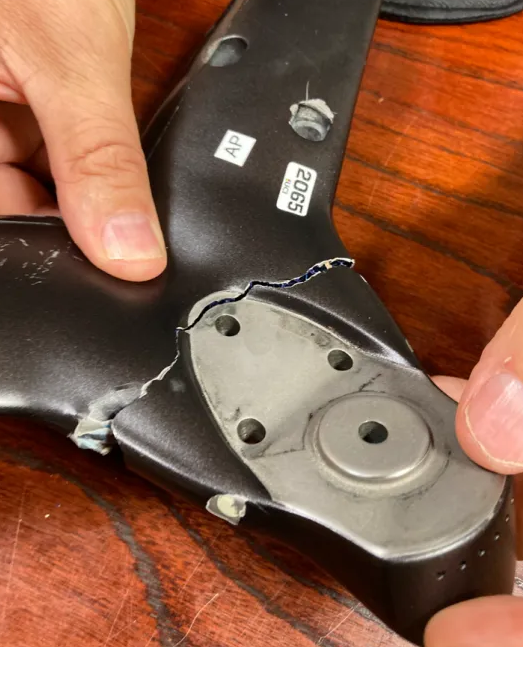
I highly recommend you read the entire article!
Designer’s Corner
Marc Raibert (Boston Dynamics) on robotic actuator tradeoffs
The founder and former CEO of Boston Dynamics was on Lex Fridman’s podcast recently. I found this discussion of the tradeoffs between electric and hydraulic actuation in robots to be particularly interesting!
Having used both of these technologies I wanted to provide a more in depth summary for you dear readers! I’ve always been quite partial to hydraulics because they have incredible power density and the advantage of decoupling the actuator from the pump/motor system. This allows them to be employed in applications where you don’t have much room for an actuator, but you still need high force capacity. Airplane control surfaces are the perfect example.
Having said that, I’ve never worked on a hydraulic system that didn’t leak at some point 😕
For all you design nerds that might have to make a tradeoff decision between the two, here's a comparison table to help you out.
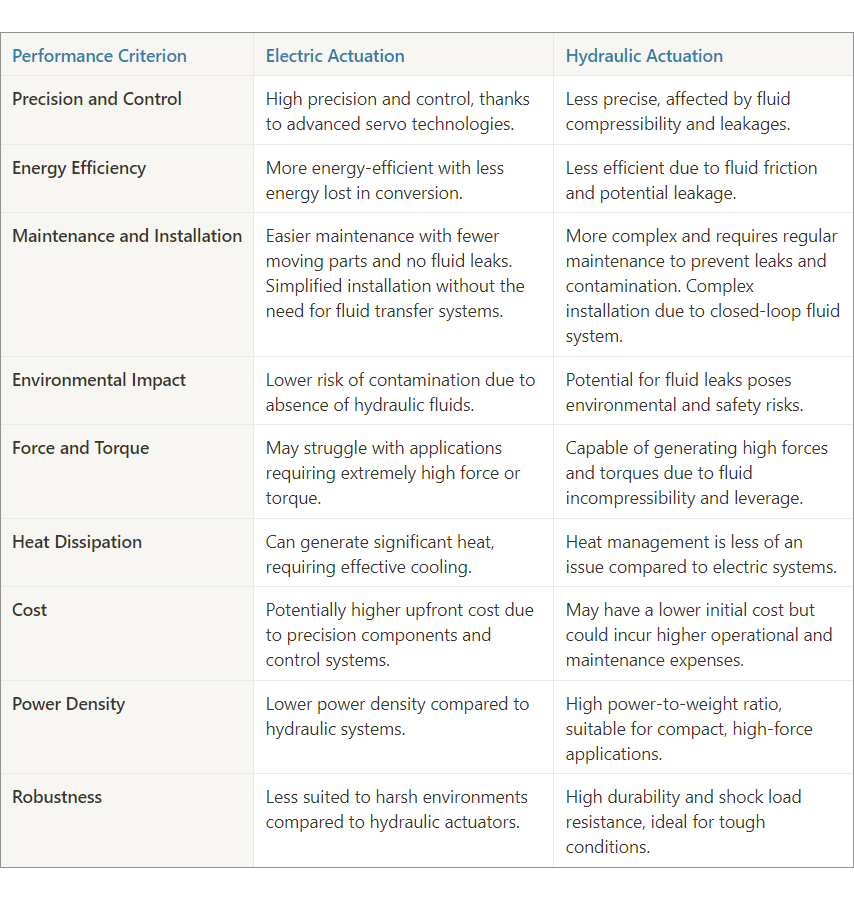
EV motor architectures and the skin effect
The folks at Munro Live go deep on stranded vs bar windings in electric motors. I really like their explanation of the skin effect in larger conductors.
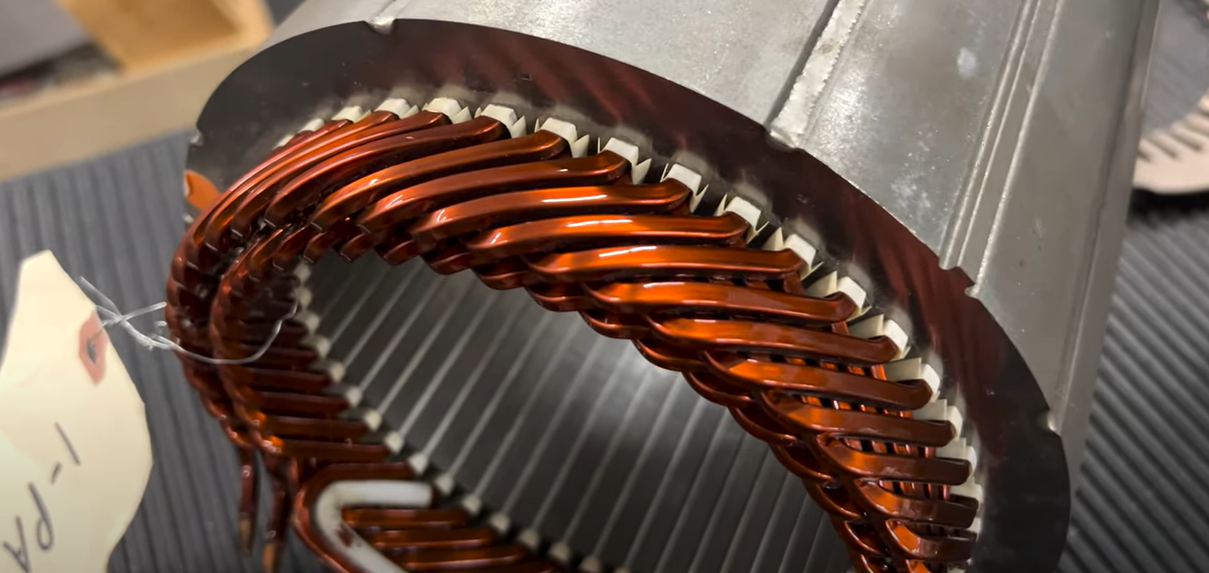
Also, don’t neglect this gem of a comment from the YouTube community on the video.
“2 things you don't mention about AC winding losses: first, the reduction to 1/3rd at skin depth, there is also a PHASE SHIFT in the current, being retarded about 60° at one skin depth, & this reduction in amplitude & phase shift continues as you move inward. But there is a second effect when a bunch of wires carrying current in the same direction are packed together. There is a loss which makes the resistance rise TO THE 4TH POWER OF THE FREQUENCY. This is because of the magnetic field in SURROUNDING conductors. Butterworth wrote about this in the 1930's as it applied to wound radio antennas, & showed that cheap radios, having antenna coils wound with thinner wire, actually performed better than the antennas in the expensive radios. I ran into this when working with Rockwell International making magnetic bubble memories in the 1980's, which have 2 quadrature driving coils (like 2-phase motor). Rockwell's coils used 1mm x 1mm square wire & had 3 times the loss of my 28-strand coils of the came cross-section. Another thing about bar-wound coils. Most of the stock for these are made from existing round wire, rolled square AFTER INSULATING & heat-treating. The copper is overworked & this raises resistivity. The wire needs to be brought to the same state in cold-working as round wire, but manufacturers selling square wire don't do that. Does Tesla have enough "pull" to get manufacturers to properly heat-treat wire BEFORE insulating?”
In case you missed it
We dropped a new engineering article last week on How to Design and Manufacture Anodized Aluminum Parts. Worth a read if you haven’t spec’d a coating in awhile!
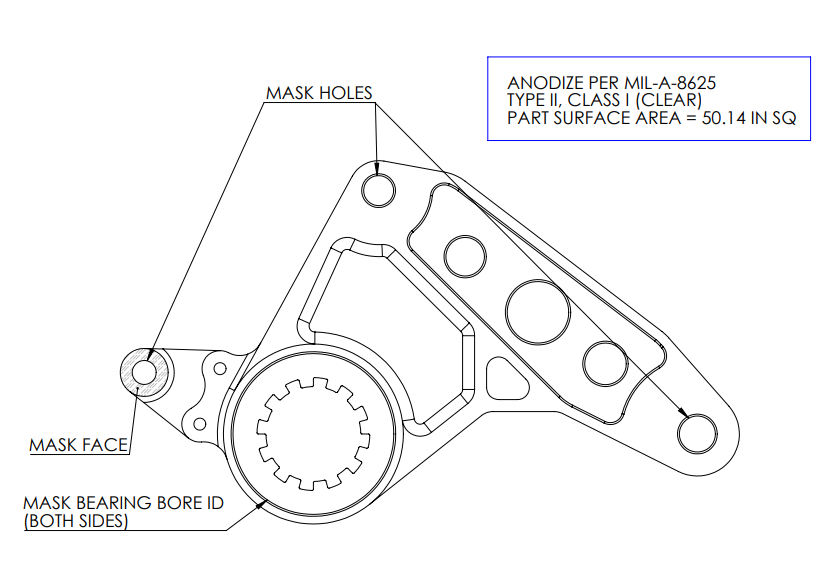
Coming soon - Five Flute Lite!
Big changes are afoot! We’ve listened to our users and will be launching a simplified version of Five Flute targeted at individuals, small agencies, and freelancer groups that want to share CAD and get fast design feedback from other engineers, clients, and manufacturers.

We’re excited about this plan because it makes it even easier to get started with Five Flute. If you want to lock in early access to Five Flute Lite, just email us and put "Lite" in the subject line!
That’s it for this issue, thanks for reading and good luck with your hardware projects!